Rubber hygiene
作者:admin 点击次数:22 发布时间:2025-04-22
Rubber is divided into two types: natural rubber and synthetic rubber. Its toxicity comes from the monomers and additives in the rubber base. Natural rubber bases include latex, smoked rubber sheets, air-dried rubber sheets, white wrinkled sheets, brown wrinkled sheets, etc. Brown wrinkled sheets have more impurities and poor quality; and smoked rubber sheets may contain polycyclic aromatic hydrocarbons after being smoked, so they cannot be used to produce rubber products for food. Synthetic rubber mainly includes silicone rubber, butadiene rubber, ethylene-propylene rubber, styrene-butadiene rubber, nitrile rubber and fluoroprene rubber. The chemical composition of silicone rubber is polydimethylsilane, which has stable chemical properties and low toxicity and can be used in the food industry. Butadiene rubber is polymerized from isoprene and isobutadiene, and ethylene-propylene rubber is polymerized from ethylene and propylene. They are widely used to make rubber products for food, but isoprene, isobutadiene, ethylene, and propylene all have anesthetic effects. Styrene-butadiene rubber is copolymerized from butadiene and styrene. Styrene monomer is toxic, but the polymer itself is non-toxic and can also be used to make rubber products for food. Butadiene rubber is made by copolymerization of butadiene and acrylonitrile, but acrylonitrile monomer is toxic. Chloroprene rubber is made by polymerization of dichloro-1,3-butadiene, and local contact with dichloro-1,3-butadiene monomer is carcinogenic, so it cannot be used to make rubber products for food.
A large amount of additives must be added to rubber during processing and molding. The vulcanization accelerator hexamethylenetetramine (accelerator H) can decompose formaldehyde when heated, while ethylenethiourea is carcinogenic and diphenylguanidine is toxic to the liver and kidneys. The aromatic amine antioxidant phenyl B-naphthylamine (anti-aging agent D) contains B-naphthylamine, which can cause bladder cancer. N,N-diphenyl-p-phenylenediamine can also be converted into B-naphthylamine through metabolism in the body. Carbon black, a commonly used filler for rubber products, contains more B(a)P. (III) Hygiene issues of coatings
Depending on the different objects of use and film-forming conditions, coatings are divided into two categories: non-high-temperature film-forming coatings and high-temperature curing film-forming coatings.
1. Non-high temperature film-forming coatings
Non-high temperature film-forming coatings allowed for use in my country include polyamide epoxy resin coatings, perchloroethylene coatings, phenol coatings, etc. These coatings must be rinsed with clean water after film formation before use. Epoxy resin is polymerized by bisphenol A and epichlorohydrin, and polyamide is the curing agent of epoxy resin coatings. The hygienic issues of polyamide epoxy resin coatings mainly involve the quality of epoxy resin (containing incompletely polymerized monomers), the ratio with the curing agent, the degree of curing, and the migration of uncured substances (including additives) into food. Perchloroethylene resin contains vinyl chloride monomer, and there may still be residual chloroethylene after curing. Free phenol and formaldehyde in urushiol coatings can migrate into food.
2. High temperature curing film-forming coatings
Commonly used are epoxy phenolic coatings, water-based modified epoxy coatings, silicone anti-stick coatings and organic fluorine coatings. After epoxy phenolic coatings are formed, the coating film may still contain unpolymerized monomers and low molecular weight polymers such as free phenol and formaldehyde. Water-based modified epoxy coatings also contain epoxy phenolic resins, so they may also contain free phenol and formaldehyde. Silicone anti-stick coatings are a relatively safe anti-stick coating for the inner wall of food containers. Organic fluorine coatings include polytetrafluoroethylene, polytetrafluoroethylene, polyhexafluoropropylene coatings, etc., with polytetrafluoroethylene being the most commonly used. Although polytetrafluoroethylene is a relatively safe coating for the inner wall of food containers, due to the high requirements for the cleanliness of the coated blanks, the bad materials are often treated with chromate before spraying, resulting in chromium salt residues in the coating. Polytetrafluoroethylene will decompose at 280°C to produce highly volatile toxic fluorides, so the temperature during use must not exceed 250°C.
(IV) Hygiene of composite packaging materials
Processed foods that require high barrier protection, as well as vacuum packaging, inflatable packaging, etc., generally use composite packaging materials that require more than one layer of high barrier materials to be added to the multi-layer composite material. High barrier materials include aluminum foil, nylon, polyester, polyvinylidene chloride, etc. There are many varieties of composite packaging materials. The most commonly used ones are based on flexible packaging materials such as paper, cellophane, plastic film, and metal foil. The soft composite film obtained by various composite processing methods, such as composite food packaging bags made of polyester-aluminum foil-polypropylene three-layer film composite. Food packaging bags made of paper, plastic film or aluminum foil with adhesives (polyurethane and modified polypropylene) include cooking bags and ordinary composite bags. The sanitation of composite packaging materials should be considered from the following two aspects.
1. Sanitation of raw materials
The raw materials such as plastic film, aluminum foil, paper, and adhesives used should meet the corresponding sanitation requirements and sanitation standards. The intermediate toluene diisocyanate contained in polyurethane adhesives can be hydrolyzed under acidic and high temperature conditions to produce carcinogens such as toluene diamine.
2. Hygiene of composite food packaging bags The layers are peeled off due to weak adhesion, and cracks and holes appear, which may contaminate food; colored inks are printed on the food contact surface of the packaging material, causing contamination to the food; during compounding, the ink and the solvent in the adhesive are not fully dried before bonding, and the residual solvent migrates to the food.
(V) Hygiene of other packaging materials
1. Ceramics and enamel
The main hygiene problem is caused by glaze. The chemical composition of glaze is metal oxides, and harmful metals will dissolve and contaminate food. Therefore, the hygienic standards for ceramic and enamel tableware containers stipulate the dissolution limits of lead and cadmium, and the limit of antimony is also increased for ceramic tableware containers. Long-term contact with acidic foods and wine such as vinegar and juice can easily cause a large amount of harmful metals to dissolve.
2. Metal products
The main hygiene problem is the dissolution of harmful metals into food. Different types of stainless steel have different components and characteristics. Containers for storing food and food processing machinery should use austenitic stainless steel (1Cr18NigT, 0Cr19Ni91Cr18N;9), and the content of lead, chromium, nickel, cadmium and arsenic should be controlled; various tableware should use martensitic stainless steel (0Cr13, 1Cr13, 2Cr13, 3Cr13) to control the content of lead, nickel, cadmium and arsenic.
Aluminum used to make food containers and packaging materials can be divided into refined aluminum and recycled aluminum. Recycled aluminum has a complex source and high impurity content. It cannot be used to make food containers. It can only be used to make cooking utensils such as spatulas and rice spoons, and attention should be paid to the source of the recycled aluminum. Harmful metals that need to be controlled in aluminum products include lead, zinc, arsenic and cadmium. Epidemiological surveys and animal experiments have found that aluminum is a risk factor for Alzheimer's disease that cannot be ignored. Long-term use of aluminum products to hold salt and alkaline and acidic foods can easily corrode the aluminum oxide protective film on the surface of the container.
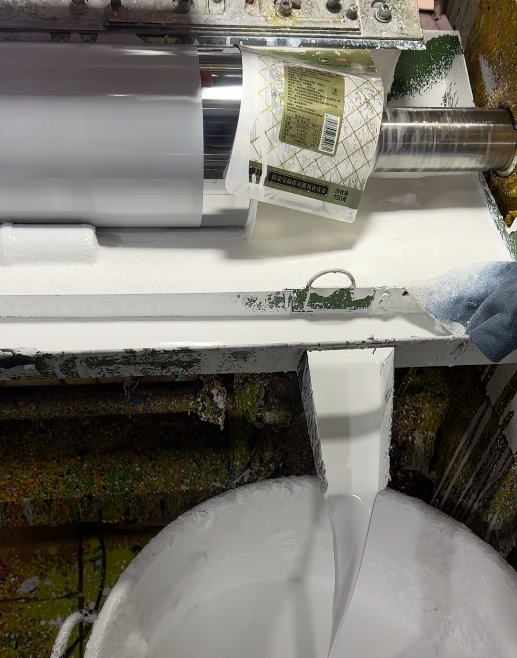